TECHNOLOGY

DESIGN
The traces of modern lines and classical design concept complement each other in each ARCEO product.
FEA strength simulations, assembly controls and weight optimization studies are carried out simultaneously on the 3D design designed with CATIA programs.
At the end of the 3D design process, our most advanced wheel designs are obtained, free from potential casting defects and providing maximum efficiency.
CASTING
ARCEO Wheels are high strength aluminum and silicon alloy wheels that have passed Radial Fatigue, Dynamic Fatigue, Impact, Impact and Corrosion tests in accordance with TSE and ISO standards.

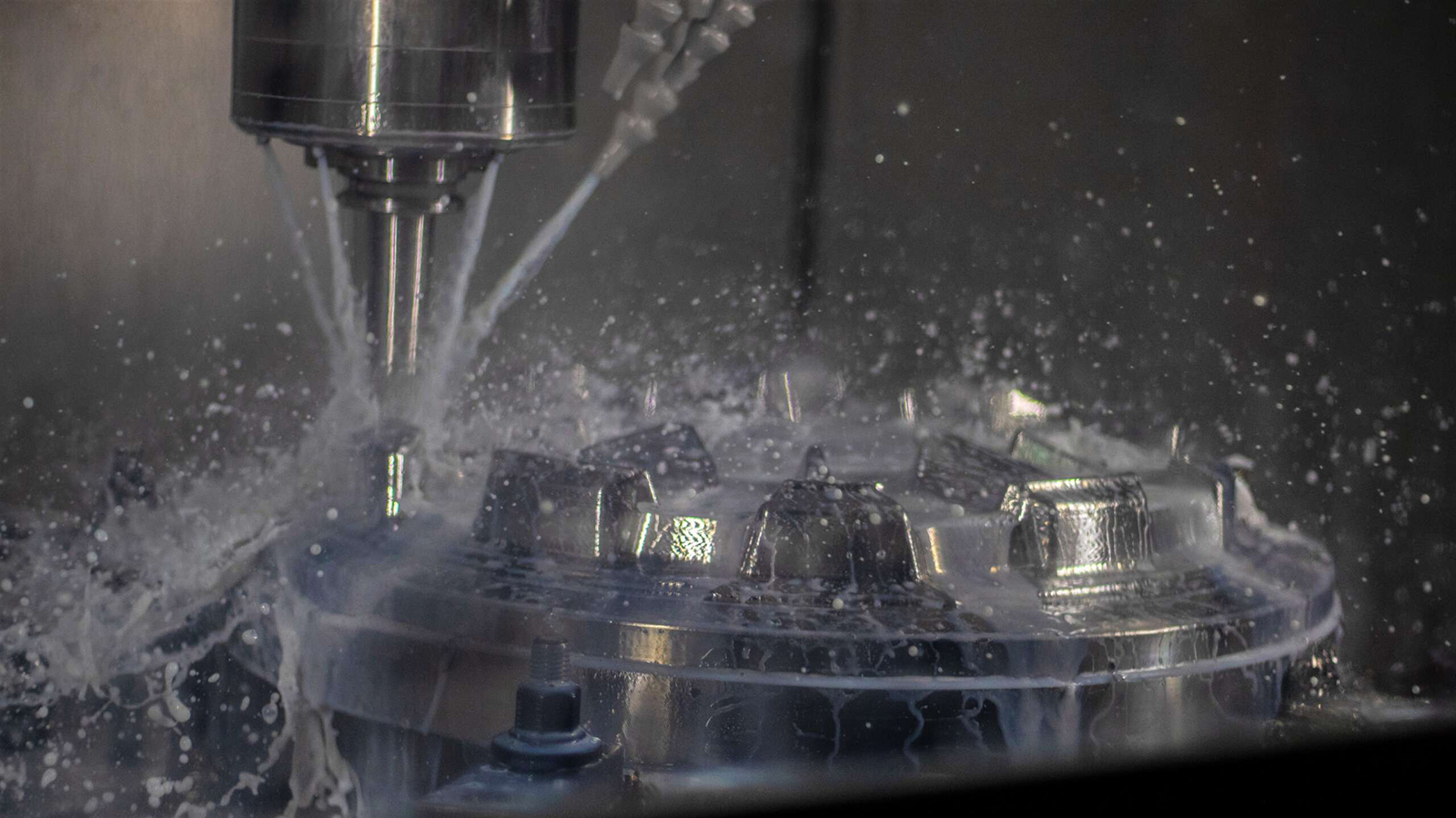
Molding
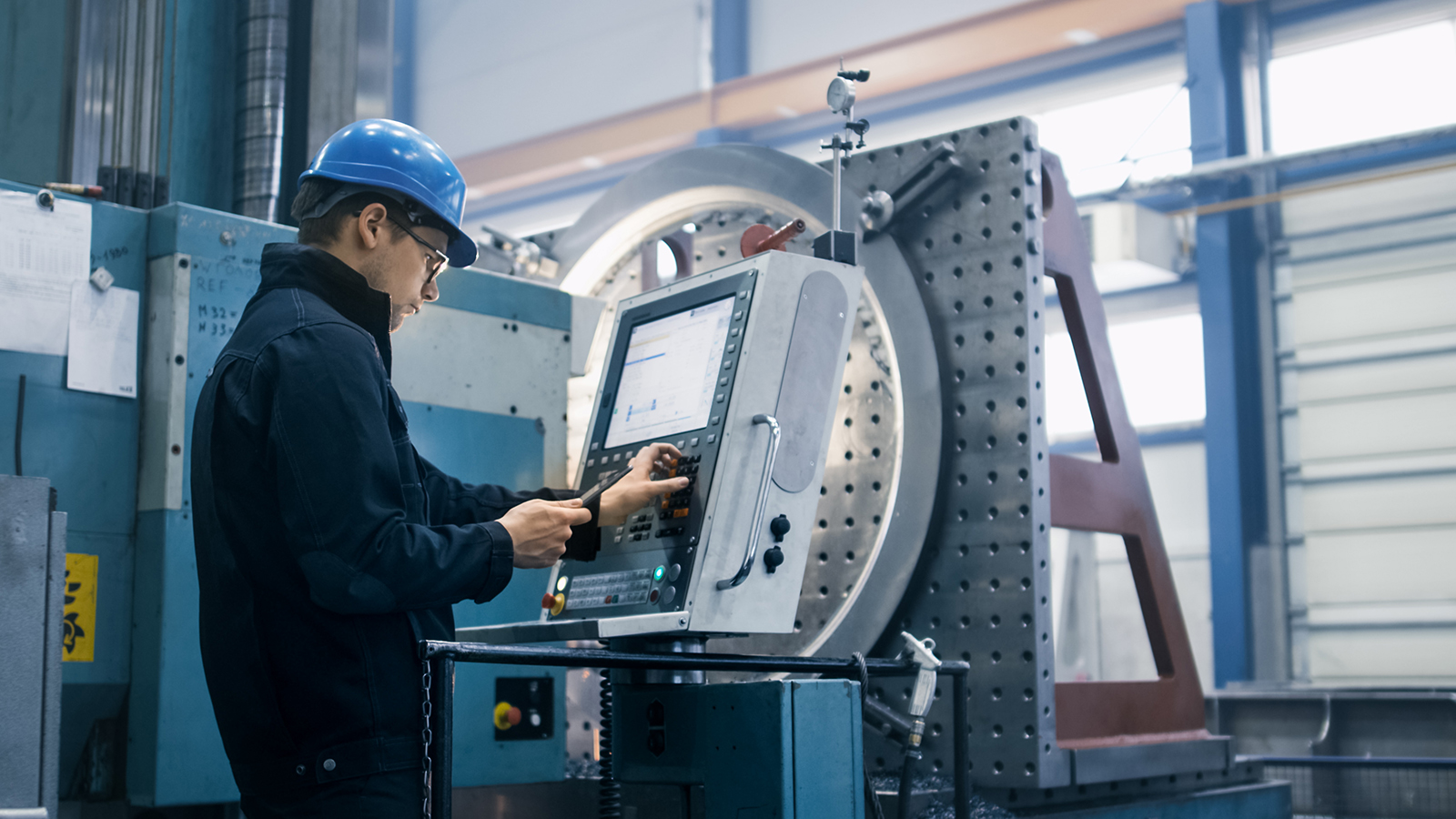
Production
ENGINEERING
Pressure: All ARCEO models are compatible with the tire pressure monitoring system (TPMS).
These measuring devices show the temperature and pressure inside the tire.
It processes and sends data so that it can be viewed on the dashboard.
DRIVING COMFORT
Alloy wheels increase driving comfort. With this awareness, our focus is always quality while producing our wheels.
Aluminum alloy, as a good conductor of thermal energy, provides the best way to dissipate the heat generated during braking. When designing our ARCEO products, we care about the easy access of air to the rim structure and cooling the disc brake.
LIGHTNESS AND PERFORMANCE
The most important advantage of alloy wheels is their durability. Our main priority is to provide durability and performance at the highest level while producing lightweight wheels. Wheels and tires are vehicle components that are not supported by the suspension.
The lighter weight of these components means a better driving experience when accelerating and cornering. In addition, with the lightness, better performance and more economical fuel consumption are provided from the vehicle.
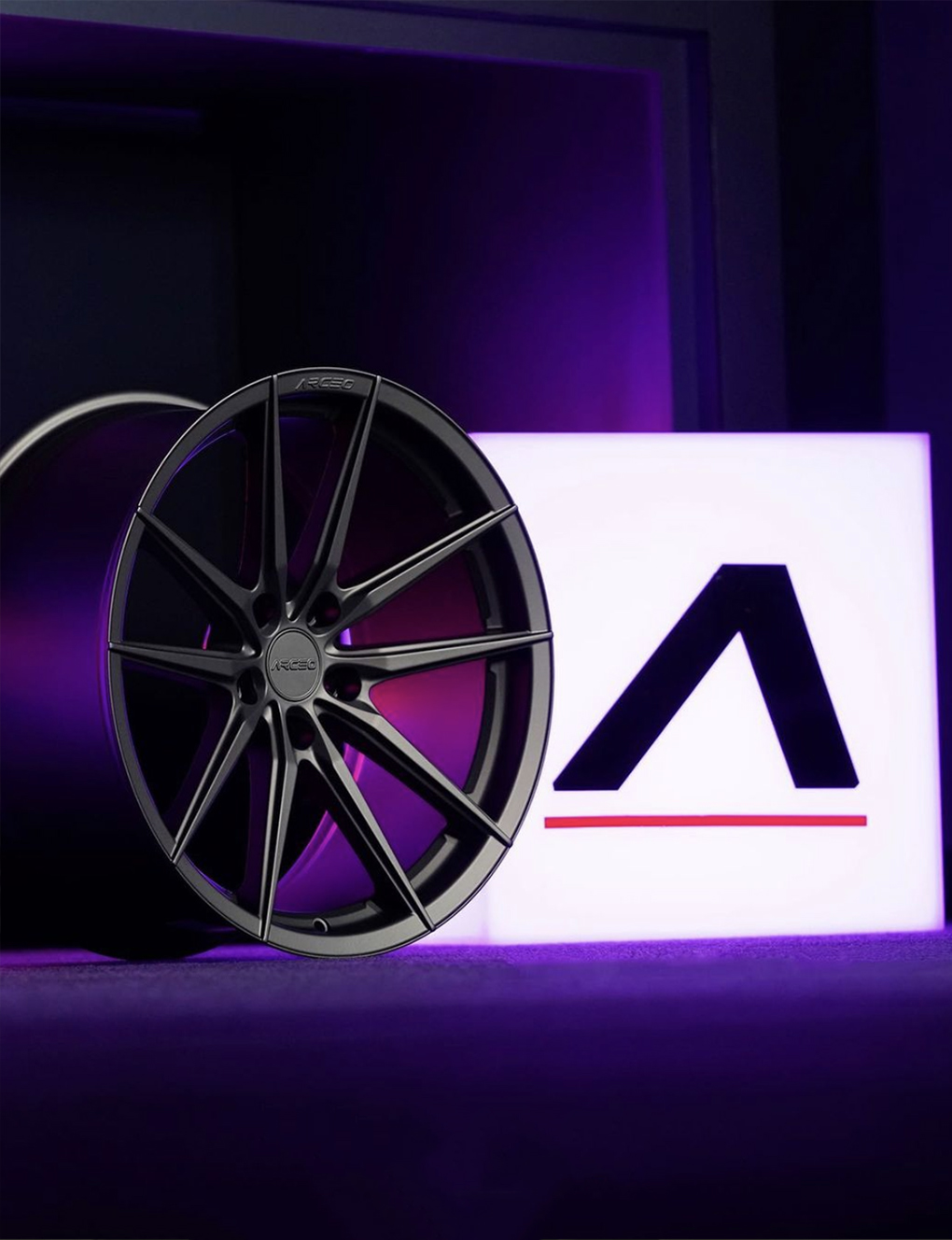